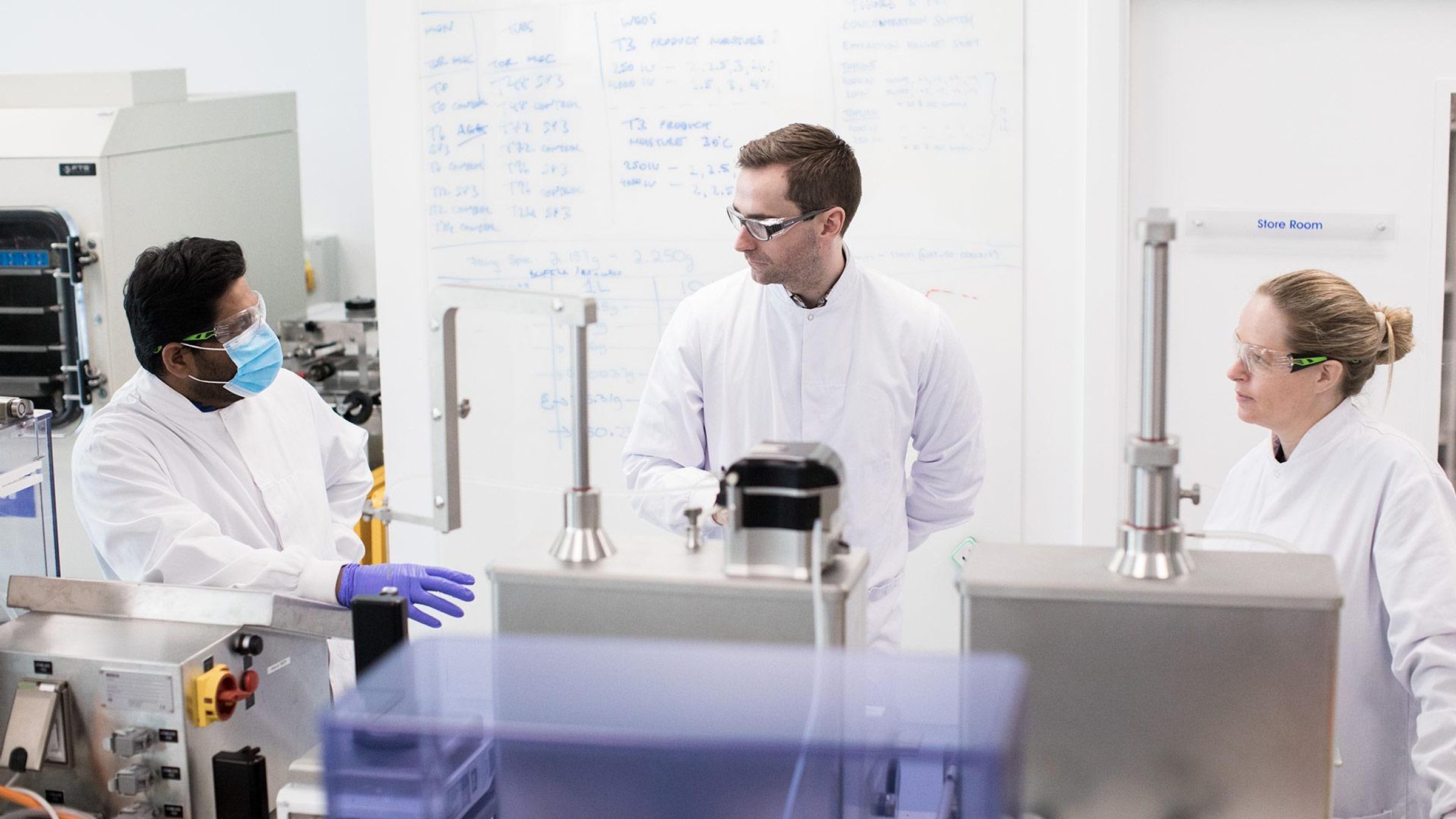
Manufacturing and Supply are the bridge between the science that happens in the research laboratories and the people and communities we serve.

Brendan O’Callaghan
Executive Vice President of Manufacturing and Supply
Our Ambition
We’re committed to raising the bar for manufacturing and supply. With sustained investment, we’re building a global network that brings together talented people and cutting-edge technologies and data to deliver high-quality, affordable, sustainable medicines and vaccines.
4.8 billion
units of medicines and vaccines produced annually*
€1 billion
170
* Includes in-house and outsourced manufacturing
Cutting-Edge Manufacturing Technologies and Data
As our R&D teams pursue transformative medicines using data, AI, and advanced technologies, our manufacturing teams are taking vaccine and biologic production to the next level.
Our new Evolutive Vaccines Facilities in France and Singapore will be fully digital and flexible, ready to deploy multiple technologies. That will help us respond swiftly to future pandemics while bringing innovation to public health faster.
Accelerating Our Pace to Chase the Miracles of Science
Inspired by McLaren’s high performance in a fast-paced environment, we’re optimizing our manufacturing and supply operations. This partnership will accelerate our chase to discover the miracles of science to improve people’s lives all over the world.
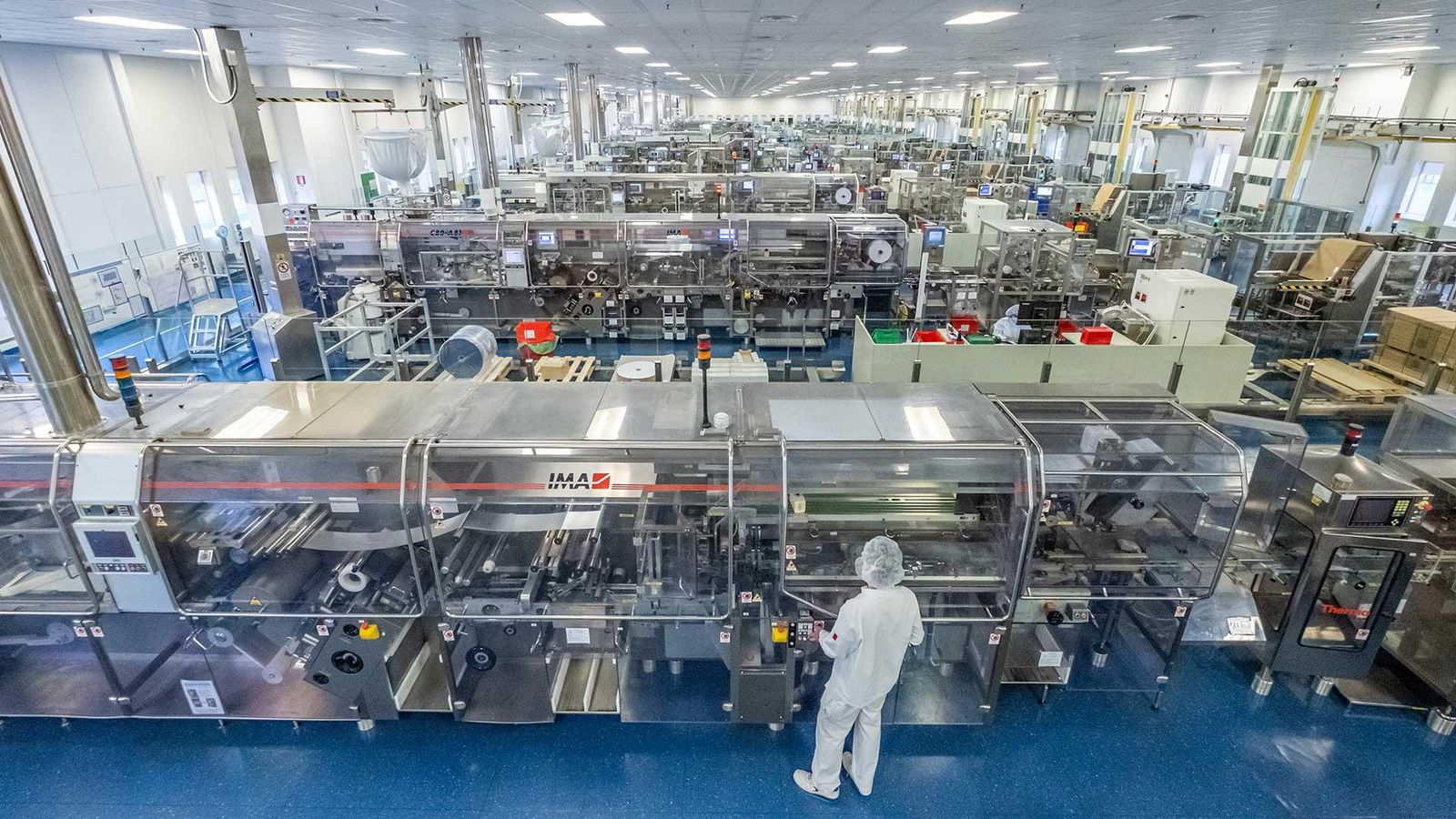
Analytics and expertise make Formula 1 pitstops an icon of efficiency. We’re adapting McLaren’s approach to model simulations of our changeovers and operations on more than 100 production lines, across all technologies.
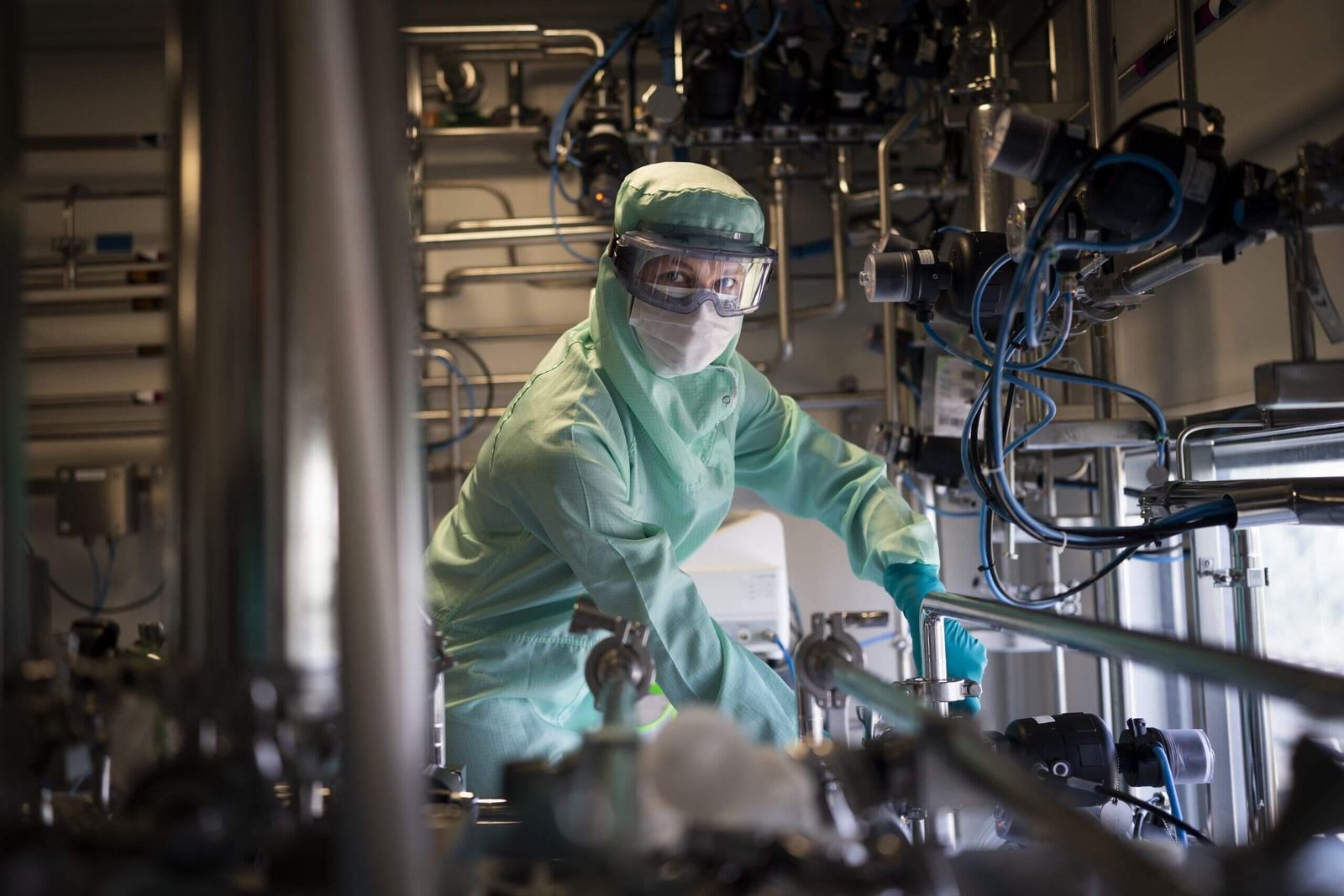
Our Expertise in Vaccine Manufacturing
Our AI-powered, state-of-the-art manufacturing sites are the bridge between scientific advances and transformative immunizations serving millions of people around the world.
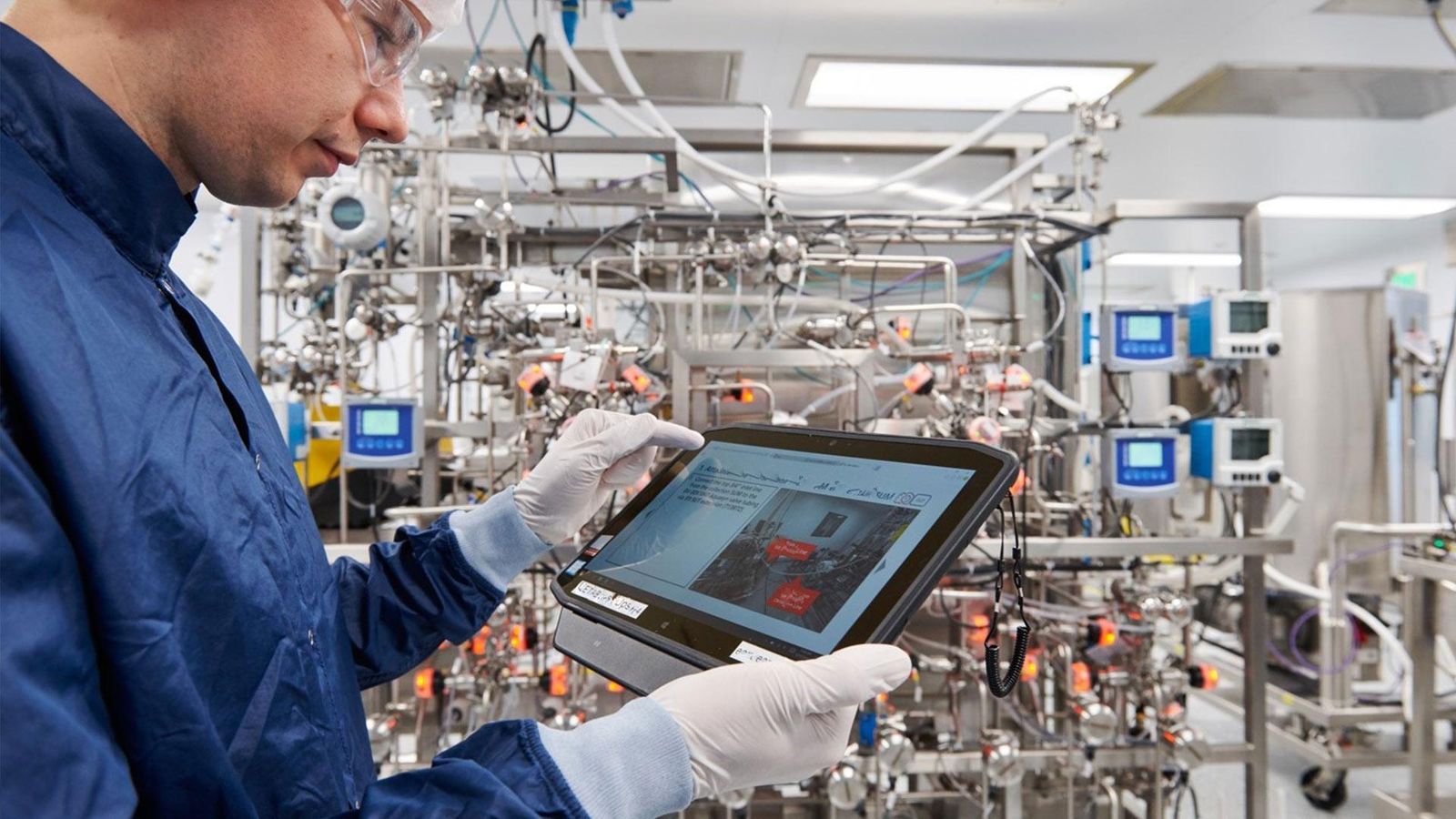
And our sites are Award winners. Our award-winning site in Framingham, MA is among the world’s first digitally enabled facilities to use continuous-biologics-production technology. Its end-to-end platform uses millions of points of data captured by sensors to continuously optimize for excellence.
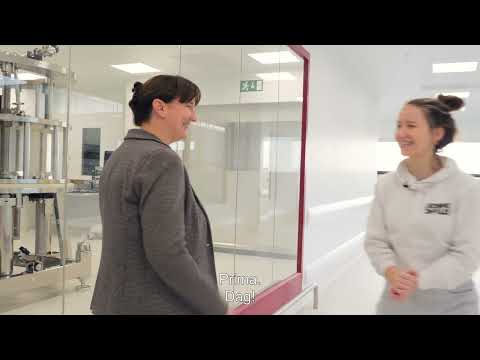
Factory of The Future Awards 2023: Sanofi
Our Belgium colleagues in Geel received the 2023 Future of the year Award. Digital technology is used to collect data in conjunction with science to improve and accelerate the production of innovative biologics. Machine Learning, Artificial Intelligence and cobots in the labs are used to take on repetitive tasks to free up analysts’ time for added value tasks. And our Geel site has a 'paperless' production and labs.
Sustainable Manufacturing and Supply
We’re committed to achieving carbon neutrality by 2030 and have built our path to net Zero emissions by 2050. That means reducing emissions across our full value chain.
55%
30%
100%
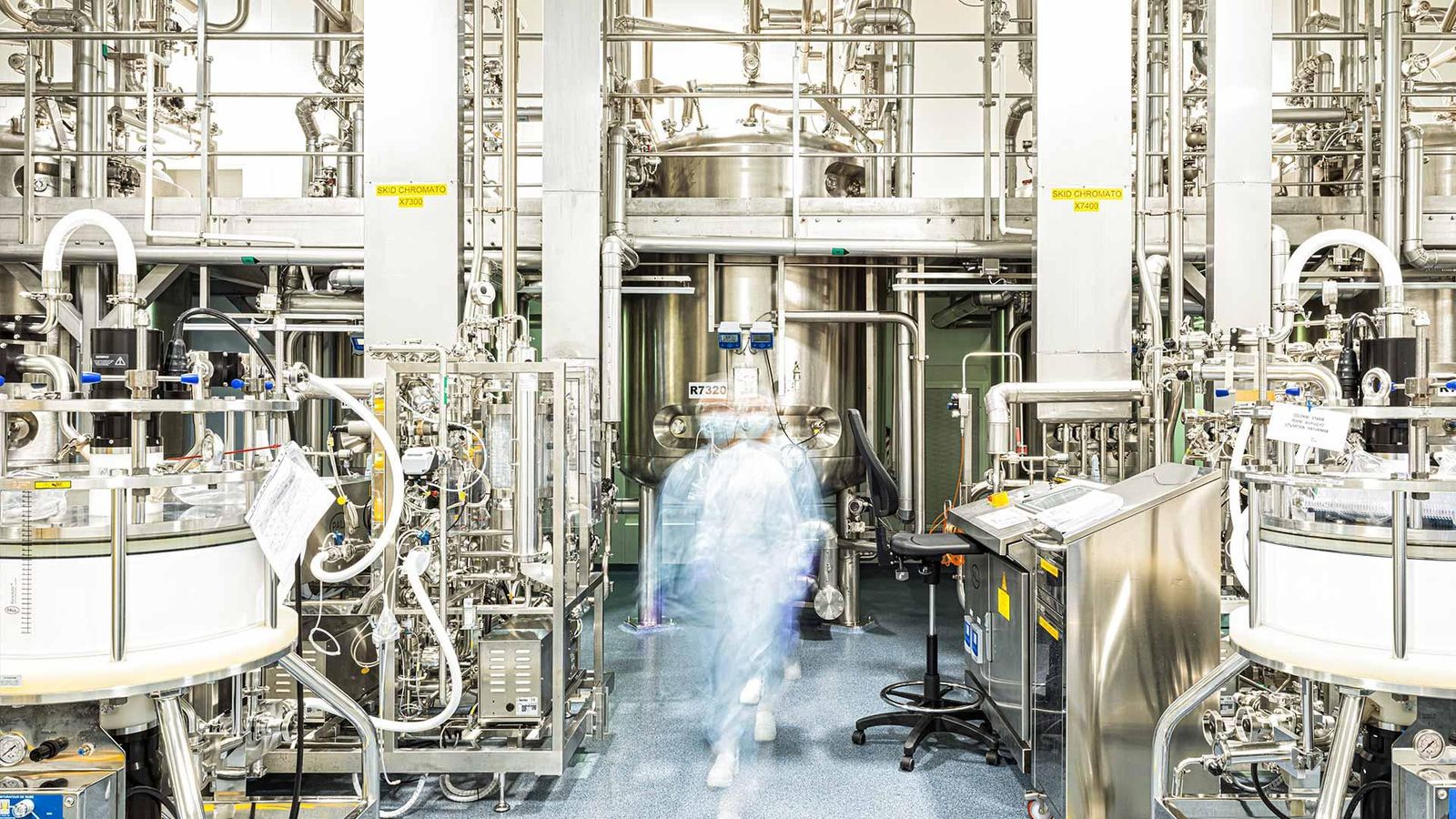
Streamlining for Planet Care
We’re limiting our environmental footprint beyond our four walls by taking action both within the company and with our suppliers. And we’re committing to improve the environmental profile of our products. For example, our eco-design approach covers the full life cycle of our products, from raw material extraction and transformation to manufacturing, transportation, and disposal.
Explore More
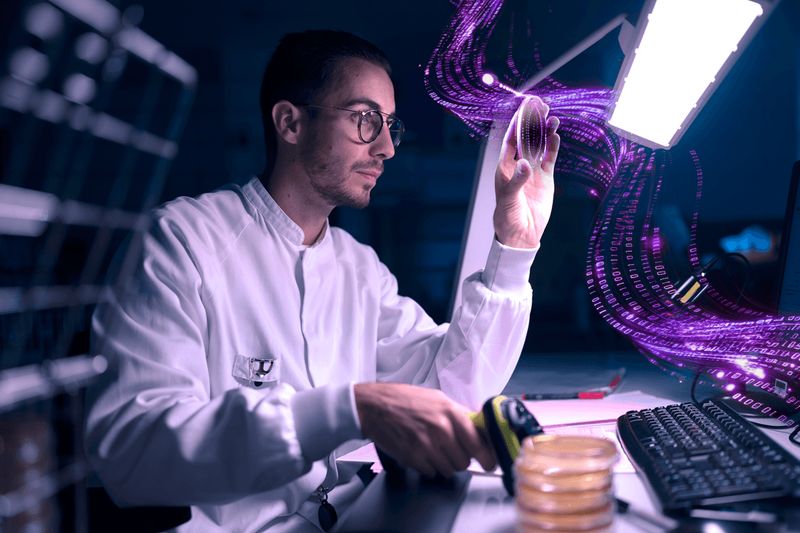
A New Era of Biopharma Production with Al
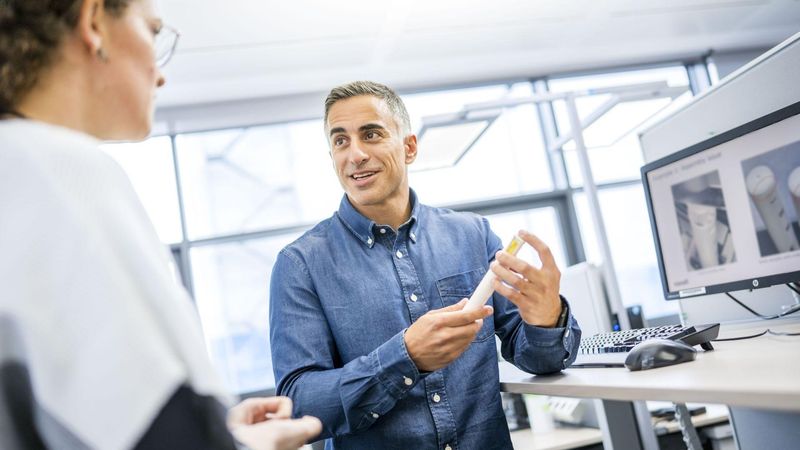
Why Patient Engagement is Critical to Manufacturing & Supply
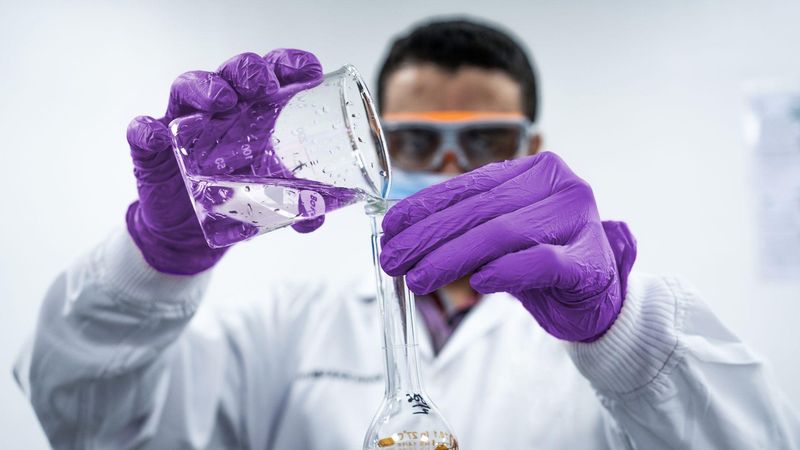